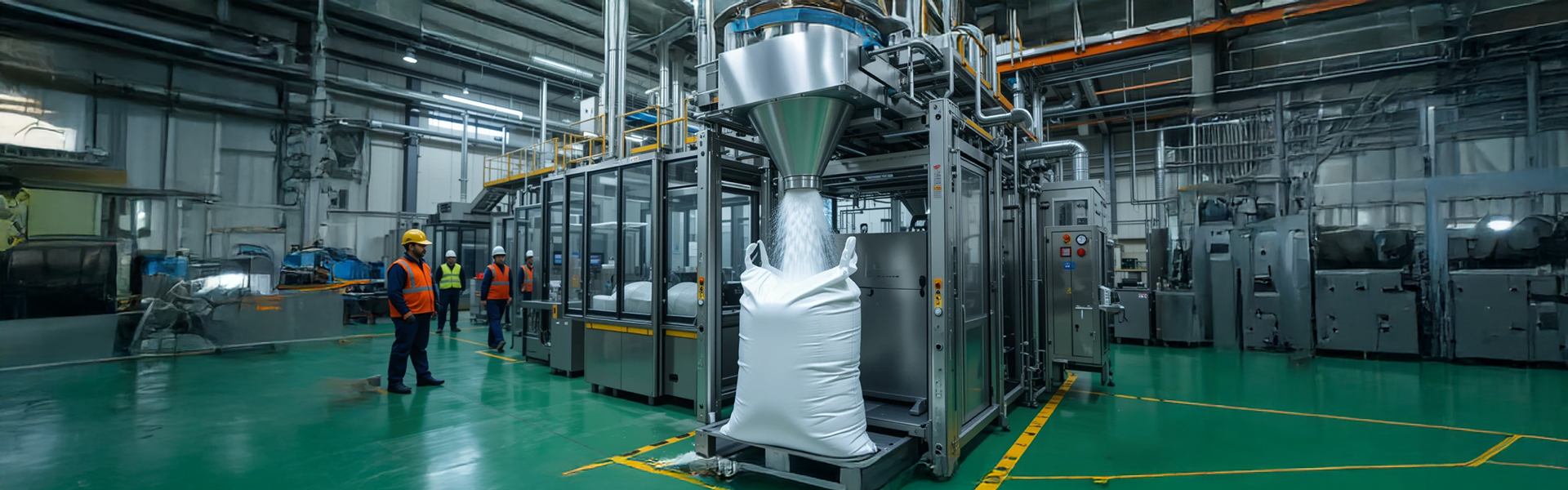
Sugar Packing Isn’t Sweet Anymore Unless You Automate Like This
The sugar packaging market is estimated to be USD 5.02 billion in 2024 and is expected to reach USD 7.95 billion by 2033, with a CAGR of 5.5% from 2026 to 2033.
Long story short, while sugar is still sugar, how you package it needs to change to meet modern throughput, hygiene, and profitability standards. Automation is quickly becoming the baseline standard in this industry.
Manual Packing: The Real Costs Behind the Bags?
Many small and medium mills still do manual or semi-manual packaging because the upfront costs appear cheaper. But the hidden costs are immense:
- Inconsistency in weights: If you overfill by just 1% over thousands of tonnes of product, that’s lost product worth tens of thousands of dollars a year.
- Rate of production: A manual filler or hand sealer cannot keep up with today’s dispatch targets, missing deadlines and making for unhappy clients.
- Contamination risk: Open filling and humans in contact with food are already raising concerns about food safety, and this will increase the number of audits you face.
- Labor costs: High turnover of skilled packers means constant training, more errors, and downtime when packers are absent.
These unrecognised losses build upon themselves, eroding margins that could otherwise have been used to expand or be more competitive on price.
What Modern Sugar Packing Machines Deliver?
Today’s automatic sugar packing machines are designed to eliminate these pitfalls. A typical integrated system includes:
- Precision weighers: Net and gross weighers designed for bulk or retail packs, which have been calibrated to weigh to within ±0.2%.
- Bag placing modules: Robotic arms, or pick-and-place units, are designed to place bags where they need to go without human interaction (human error).
- Enclosed, dust-free filling: Specifically designed auger or gravity fillers minimize spilling and protect product quality.
- Secure bag closing: Heat sealing, stitching, or gluing keeps leaks and pilfering to a minimum during handling and shipping.
- Inline QA checks: Metal detectors and checkweighers verify that every bag meets specifications before leaving the line.
With this setup, companies can offer consistent weights, uncluttered lines, and predictable output shifts, directly related to the ability to win significant supermarket or export contracts.
The Hard Numbers: Why Automation Pays for Itself
The global packaging automation market is projected to grow from USD 80.67 billion in 2025 to an estimated USD 158.60 billion by 2034, with a registered CAGR of 7.8% from 2025 to 2034. Here’s why:
- Productivity: Automated case packers, tray formers, shrink wrappers, and palletizers typically handle up to 6000 cases per hour.
- Accuracy: Vision-guided robots and automated flap folding ensure each carton is packed correctly, minimizing miscounts, rework, and damage during transit.
- ROI: Industry data shows secondary automation pays back within 12–24 months thanks to reduced labor, fewer packing errors, and consistently stable pallet loads that lower in-transit losses.
For example, Alligator’s open-mouth bagging systems are designed to handle 10–50 kg bags at up to 20 bags per minute, delivering precise fills, faster bag handling, and cleaner operations.
Which Automation Setup Is Right for You?
The best sugar packing machine depends on your volume, bag types, and flexibility needs:
- Semi-automatic case packers are practical entry points. They automatically erect and seal cartons while still requiring manual loading of filled primary packs. This reduces repetitive strain and speeds up operations.
- Fully automatic case or tray packers inflate, load, and close cartons in one integrated system. Options include top-load, side-load, or wrap-around configurations. These packers handle up to 15–30 cartons per minute, making them ideal for high-volume runs.
- Shrink-wrap or cassette tray systems add a final protective film or tray around packed cartons. Depending on the pack format, shrink wrappers can operate at 10–450 cycles per minute.
- Robotic palletizers layer and stack cases precisely onto pallets. Modern robotic systems achieve 30–100 cases per minute, enabling compact, high-throughput end-of-line packaging.
A Quick Pre-Automation Checklist
Before upgrading, sugar processors should always ask:
- What pack sizes and daily tonnage do we need to hit in peak season?
- Is our sugar free-flowing or sticky? This affects filler choice.
- How fast do we need to switch between pack sizes or bag materials?
- Do we have a clean environment and a dust extraction plan?
- Does the vendor offer robust after-sales support and local spares?
A clear checklist ensures you buy exactly what you need, not an overengineered system that stays idle half the year.
Why Choose Alligator Automation?
Alligator Automation has decades of experience engineering modular, high-performance sugar packing lines for diverse operations.
With a comprehensive secondary packaging suite that includes semi-automatic and fully-automatic case packers, shrink/tray systems, and high-speed robotic palletizing. These features include modular flexibility and integrated data monitoring. You get complete end-of-line automation that improves output, quality, and return on investment.
This suite is further enhanced by plug-and-play modularity, remote PLC monitoring, and a food-grade, dust-controlled design, which ensures clean operations and minimal downtime.
With local field engineers and spares support, Alligator offers not just equipment but a scalable pathway to high-performance secondary packaging solutions and measurable ROI.
Time to Make Sugar Packing Sweet Again
The global sugar market is competitive, so every lost gram and every extra minute on your packing line matters. Automation helps you deliver consistent, hygienic, and cost-effective packing that keeps you ahead of the curve.
Looking to upgrade? Connect with us today for a custom-designed sugar packing solution that delivers exactly what your business needs — sweet returns, year after year.
FAQs
What are the benefits of automating sugar packing?
It boosts packing speed, ensures accurate weights, cuts product wastage, improves hygiene, and lowers dependence on manual labour.How does automation improve sugar packing operations?
It standardizes filling, sealing, and quality checks, resulting in consistent bag quality and higher overall equipment effectiveness (OEE).What types of automation are available for sugar packing?
Options include semi-automatic and fully automatic case packers, tray packers, shrink-wrap systems, and robotic or gantry palletizers for efficient case handling and palletizing.Can automation reduce product wastage?
Yes, better dosing and controlled filling eliminate overfill and spillage, directly increasing yield.- How does automation improve hygiene?
Enclosed fillers and reduced manual handling mean less contamination risk, cleaner lines, and easier compliance with food safety norms.